Top 6 Manufacturing Employee Performance Evaluation Tools
-
Bella Williams
- 10 min read
Manufacturing Evaluation Tools play a critical role in enhancing employee performance within the industry. As factories evolve with technology and increasing demands, understanding how to assess workforce efficiency becomes essential. These tools help identify strengths and weaknesses, enabling leaders to foster growth and accountability among employees.
In this section, we will explore six key evaluation tools that aid in performance assessment, highlight their unique features, and explain their significance. By adopting these tools, manufacturers can create a culture of continuous improvement, aligning employee goals with organizational objectives. This approach paves the way for increased productivity and job satisfaction.
Generate visualizations from your qualitative data. At Scale.
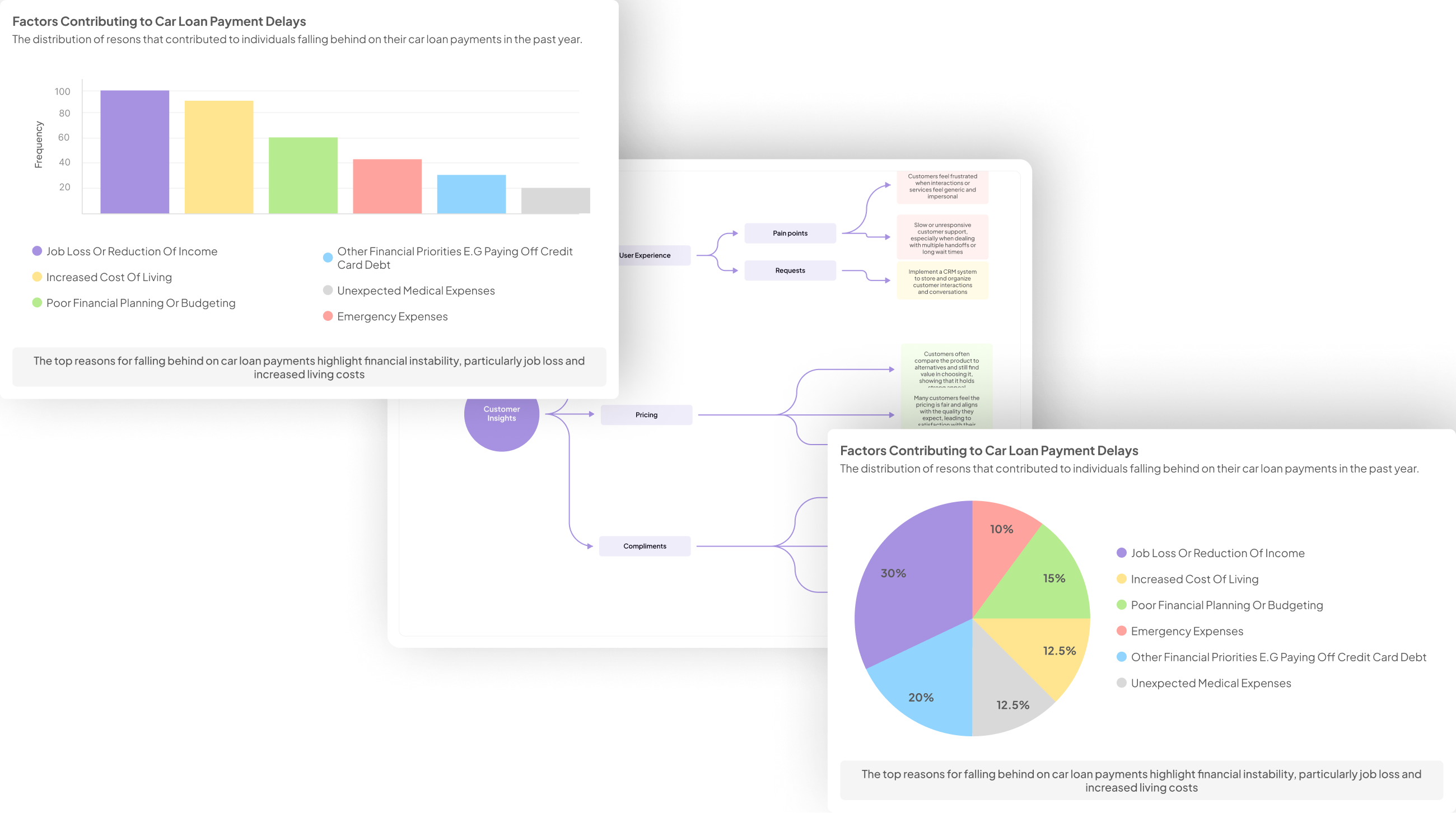
Essential Tools for Evaluating Performance in Manufacturing
Evaluating employee performance in manufacturing is crucial for maintaining productivity and quality. Essential tools streamline this process, enabling organizations to effectively gauge their workforce’s contributions. Ideally, these tools provide insights that inform management decisions, coaching opportunities, and performance improvement strategies.
A few common Manufacturing Evaluation Tools are as follows:
- Performance Appraisal Systems: These systems offer structured evaluations that assess individual contributions against established metrics. They facilitate comprehensive feedback and goal-setting sessions.
- 360-Degree Feedback: This method includes input from peers, supervisors, and subordinates, providing a well-rounded view of an employee’s performance. It helps identify strengths and areas for development.
- Key Performance Indicators (KPIs): KPIs create measurable values that indicate progress toward specific goals. These quantifiable objectives help align individual performance with the organization’s strategic goals.
- Self-Assessment Tools: Encouraging employees to assess their performance can foster accountability and self-improvement. These tools often serve as a starting point for discussions during performance reviews.
- Real-Time Performance Tracking: Implementing technology to monitor key activities helps managers identify performance trends instantly. This approach allows for timely interventions and support.
- Competency Management Systems: These tools outline the skills and competencies required for different roles. They assist in aligning individual capabilities with job expectations, thereby improving overall team efficiency.
Utilizing these tools enables a balanced and data-driven approach to performance evaluation, essential for the dynamic environment of manufacturing.
Importance of Performance Evaluation in the Manufacturing Sector
Performance evaluation in the manufacturing sector is essential for sustaining operational efficiency and enhancing workforce productivity. By implementing effective manufacturing evaluation tools, organizations can systematically assess employee performance, identifying areas for improvement and recognizing top performers. This process not only aids in aligning individual goals with organizational objectives but also fosters a culture of continuous improvement.
Furthermore, performance evaluations contribute to better communication and collaboration among team members. They provide critical feedback that helps employees understand their strengths and weaknesses, thereby guiding professional development. Additionally, regularly assessing workforce productivity can highlight trends that inform decision-making. Ultimately, robust performance evaluation practices lead to a more engaged and competent workforce, which is crucial for maintaining competitive advantage in the manufacturing industry.
How Manufacturing Evaluation Tools Enhance Efficiency
Manufacturing Evaluation Tools play a critical role in boosting operational efficiency within manufacturing environments. By implementing these tools, companies can systematically assess employee performance, identify strengths and areas for improvement, and align individual contributions with organizational goals. This strategic alignment encourages a culture of continuous improvement, leading to enhanced productivity.
Additionally, these evaluation tools facilitate data-driven decision-making by providing real-time insights into employee workflows. This allows supervisors to make timely adjustments and interventions, minimizing downtime and optimizing resource allocation. When employees receive constructive feedback based on objective metrics, they can take ownership of their performance, thus fostering a more engaged workforce. Overall, integrating Manufacturing Evaluation Tools not only enhances individual accountability but also drives collective organizational success.
Top Manufacturing Evaluation Tools for Employee Assessment
Manufacturing evaluation tools play a crucial role in assessing employee performance within the manufacturing sector. These tools enable companies to systematically evaluate key performance indicators, helping to identify strengths and areas for improvement among employees. By implementing these tools, leaders can make informed decisions based on reliable data, fostering a culture of continuous growth within their teams.
Key tools include performance management software, 360-degree feedback systems, and skills assessment platforms. Performance management software allows organizations to set clear objectives and track progress over time. Meanwhile, 360-degree feedback systems provide a comprehensive view of an employee’s performance by incorporating peer and supervisor evaluations. Finally, skills assessment platforms focus on identifying employees’ competencies, ensuring that the workforce is aligned with the organization’s goals. Each of these manufacturing evaluation tools offers distinct advantages, collectively enhancing employee assessment and driving organizational success.
Tool 1: Real-Time Performance Management Software
Real-time performance management software offers manufacturers an agile solution for evaluating employee performance. This tool allows managers to monitor employee activity and productivity continuously, providing insights that can facilitate timely feedback. By capturing metrics in real time, this software helps teams address performance issues swiftly and effectively, leading to enhanced productivity.
Evaluate Performance on Customer Calls for Quality Assurance.
Furthermore, such systems streamline performance evaluation processes, which can prove vital in fast-paced manufacturing environments. With dashboards displaying key performance indicators, managers can quickly identify trends and patterns in individual and team performance. This proactive approach not only promotes accountability but also encourages continuous improvement. Ultimately, integrating real-time performance management software into your operations adds a significant advantage among manufacturing evaluation tools, bridging the gap between metrics and actionable insights.
Tool 2: 360-Degree Feedback Mechanism
The 360-degree feedback mechanism is a powerful manufacturing evaluation tool that fosters comprehensive employee assessments. This method collects performance data from various sources, including supervisors, peers, and subordinates, providing a well-rounded view of an employeeโs skills and behaviors. By gathering insights from multiple perspectives, organizations can identify strengths and areas for improvement more effectively than traditional evaluations.
Implementing this feedback tool creates an open dialogue about performance expectations and development goals. Employees receive constructive feedback from different angles, encouraging accountability and personal growth. Moreover, organizations can tailor training programs based on the feedback received. This method not only improves individual performance but also enhances overall team dynamics and workplace morale. In manufacturing environments, such holistic approaches ensure that employees are equipped for the challenges ahead and are aligned with company objectives.
Tool 3: Key Performance Indicator (KPI) Dashboards
Key Performance Indicator (KPI) Dashboards serve as essential tools in evaluating employee performance within manufacturing. These visual representations of data capture vital metrics that reflect productivity, quality, and efficiency. By organizing data into an accessible format, KPIs allow for instant analysis and decision-making. A dashboard can reveal trends over time, helping identify areas for improvement and celebrate teams that excel.
Utilizing KPI dashboards effectively involves determining the most relevant metrics to track. Important elements include production output, defect rates, and employee engagement scores. By reviewing these indicators regularly, management can adapt strategies and make informed decisions. In addition, KPI dashboards foster transparency; employees can understand their performance relative to organizational goals. This approach not only enhances accountability but also motivates staff by providing clear performance expectations.
Advanced Manufacturing Evaluation Tools for Comprehensive Analysis
In todayโs competitive manufacturing sector, employing advanced manufacturing evaluation tools is essential for a comprehensive analysis of employee performance. These tools serve as a bridge between data collection and insightful decision-making, facilitating a deeper understanding of workforce productivity and potential areas for improvement. By systematically analyzing data, organizations can identify strengths and weaknesses across various departments.
Key evaluation tools include real-time performance dashboards, which provide instant feedback on employee metrics. Additionally, peer review systems allow for a holistic view of employee contributions through collaborative assessments. Another essential tool is skill assessment tests, which help gauge employee capabilities effectively. Each of these tools plays a vital role in enhancing workforce efficiency, ultimately contributing to overall operational excellence. By embracing these advanced evaluation methods, manufacturers can foster a culture of continuous improvement and adaptability in a rapidly evolving industry.
Tool 4: Machine Learning and AI-Driven Solutions
Machine learning and AI-driven solutions are revolutionizing the way manufacturers evaluate employee performance. By analyzing large datasets, these technologies help identify patterns that traditional methods might overlook. They provide insights into individual and team productivity, enabling organizations to tailor training programs and improve overall efficiency.
Utilizing AI algorithms, managers can pinpoint areas where employees excel or struggle. This type of analysis not only enhances performance evaluations but also assists in goal setting, leading to more focused developmental initiatives. The integration of these manufacturing evaluation tools fosters a culture of continuous improvement, ensuring that employees receive the support they need to thrive in an evolving industry. As organizations adopt these advanced solutions, they pave the way for more transparent and effective performance management systems overall.
Tool 5: Time Tracking and Productivity Tools
Time tracking and productivity tools are essential components in the realm of manufacturing evaluation tools. These tools enable businesses to monitor employee performance accurately, ensuring productivity aligns with organizational goals. By measuring time spent on various tasks, they provide a clear insight into operational efficiency and potential bottlenecks.
Effective time tracking can highlight areas where employees excel or need improvement. For example, identifying tasks that consume excessive time can help managers implement changes. Additionally, these tools can foster accountability, encouraging employees to remain focused on their work. Regular monitoring also aids in performance reviews, presenting data that influences decision-making and strategy development. By incorporating time tracking and productivity tools into their systems, manufacturers can enhance overall performance and support employees in their roles.
Tool 6: Employee Self-Assessment Platforms
Employee self-assessment platforms are transformative tools in the realm of manufacturing evaluation tools. They empower employees to reflect on their performance, set personal goals, and identify areas for improvement. By encouraging self-reflection, these platforms foster a culture of accountability and engagement within the workforce, leading to enhanced motivation.
Moreover, self-assessment platforms facilitate meaningful conversations between employees and managers. When employees take the initiative to evaluate their performance, it provides managers with a clearer understanding of each individualโs perception of their contributions. This understanding can streamline the performance review process, making it more collaborative and insightful. Ultimately, integrating self-assessment platforms into your performance evaluation strategy can drive productivity and employee satisfaction significantly. This approach not only enhances individual growth but also contributes to the overall success and efficiency of the manufacturing operation.
Generate visualizations from your qualitative data. At Scale.
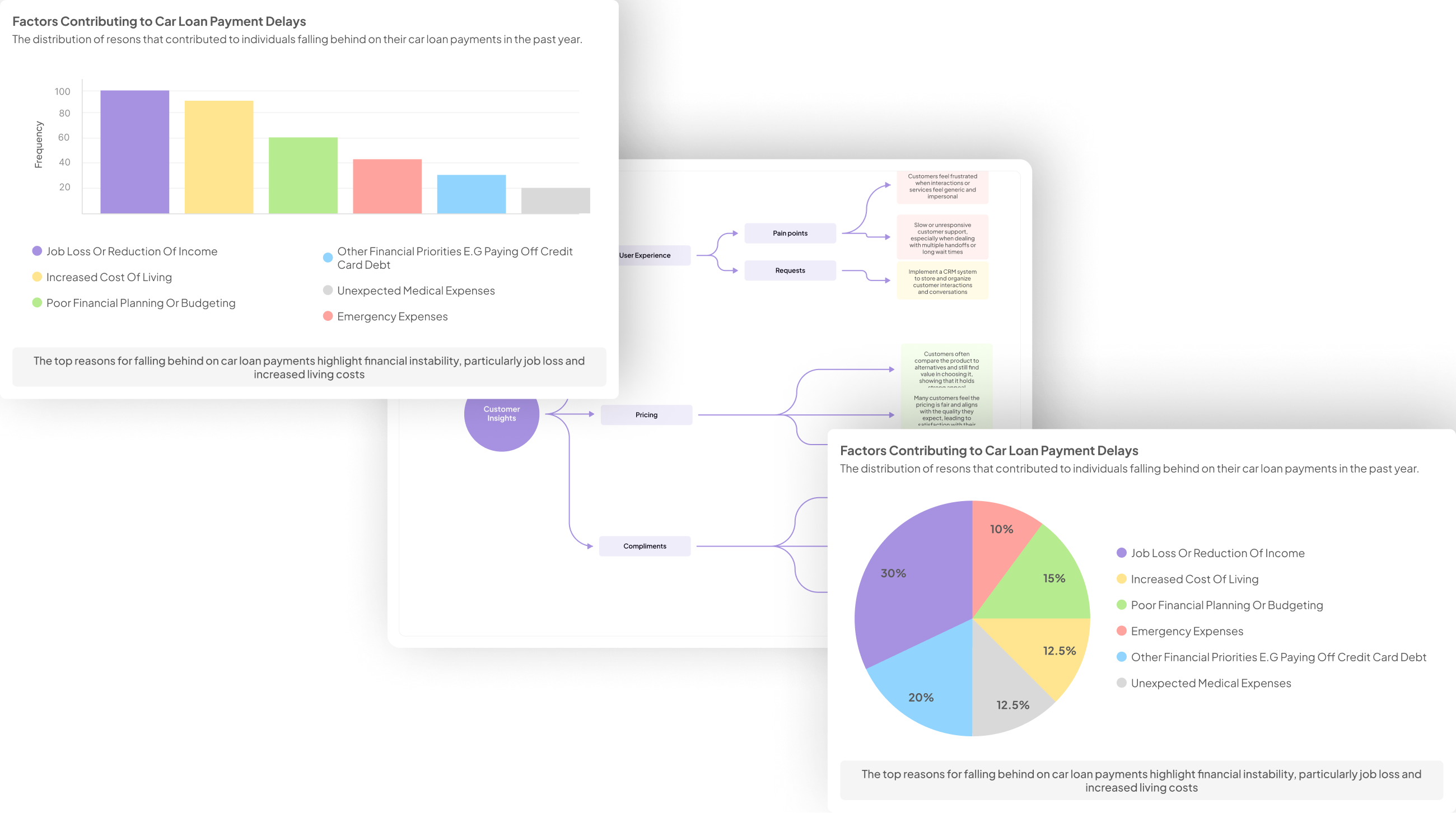
Conclusion: Maximizing Efficiency with Manufacturing Evaluation Tools
To maximize efficiency in manufacturing, implementing the right evaluation tools is essential. These Manufacturing Evaluation Tools help organizations accurately assess employee performance and identify areas for improvement. By utilizing these tools, manufacturers can enhance productivity and better align their workforce with company goals. This not only fosters a culture of continuous development but also leads to higher employee satisfaction and retention.
Moreover, analyzing performance data allows for strategic decision-making. Companies can pinpoint strengths and weaknesses among teams, ultimately streamlining training and support initiatives. In doing so, they create a robust framework for sustained growth and innovation, highlighting the critical role of effective evaluation in todayโs competitive manufacturing environment.