Effective Quality Process Improvement Tools And Techniques
-
Bella Williams
- 10 min read
Quality Improvement Tools play a critical role in today’s competitive business landscape. As organizations strive to enhance their processes, the right tools can provide the necessary framework for consistent growth and development. Using these tools allows teams to systematically identify areas for improvement, ultimately leading to better quality and operational efficiency.
In this section, we will explore various Quality Improvement Tools that serve as essential resources for effective process optimization. From methodologies like Six Sigma to the PDCA cycle, each tool offers unique benefits tailored to specific organizational needs. Understanding these tools will empower professionals not only to implement change but also to foster a culture of continuous improvement within their teams.
Analyze & Evaluate Calls. At Scale.
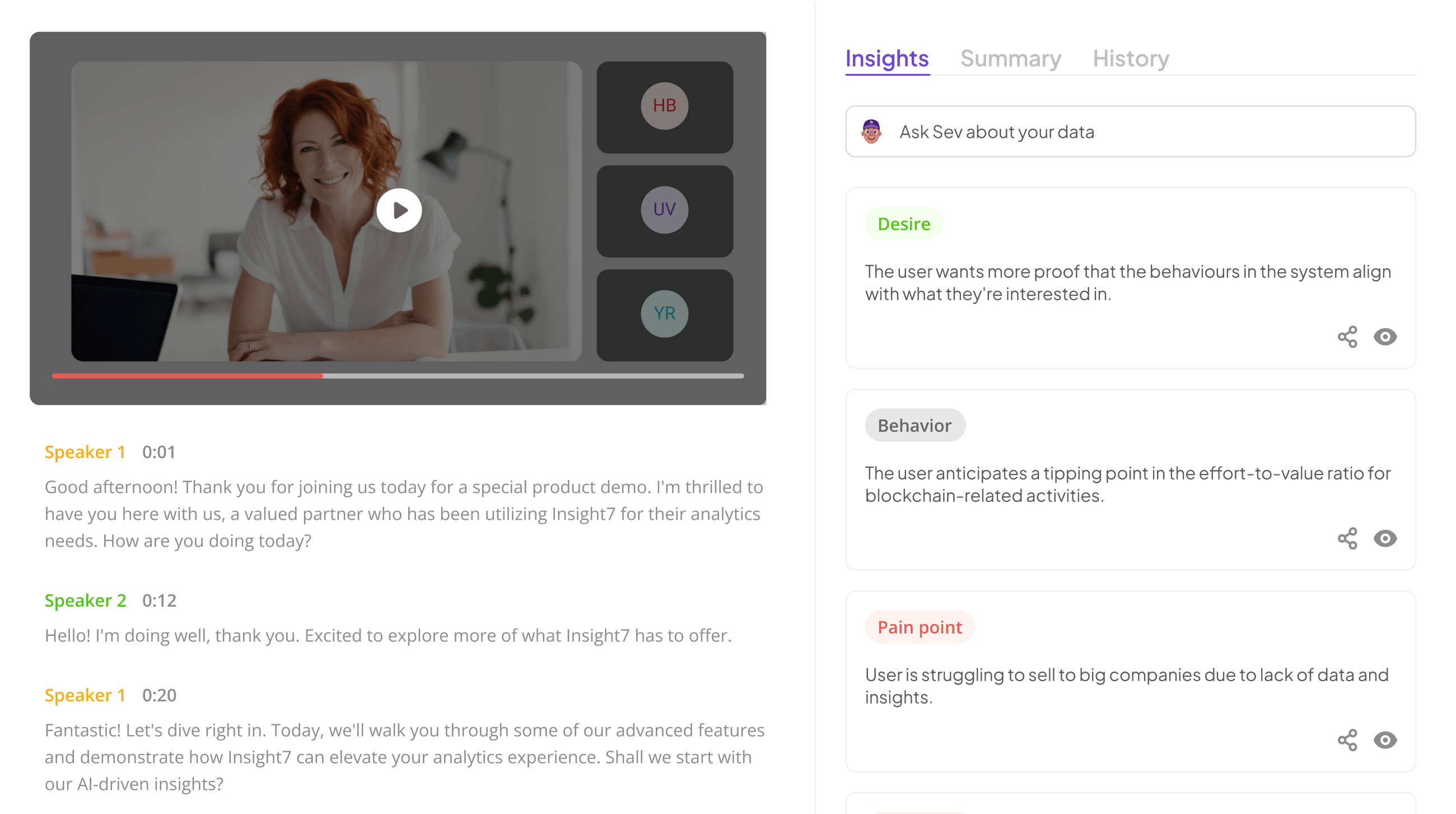
In todays fast-paced business environment, effective quality improvement tools and techniques are crucial for maintaining competitiveness. This blog will delve into some of the most effective tools for process improvement that organizations can utilize to enhance quality and efficiency.
In today's bustling business world, quality improvement tools serve as essential assets for maintaining competitive edges. Adopting effective techniques can propel organizations toward enhanced quality and efficiency in their operations. By focusing on systematic improvements, businesses can better meet customer expectations and respond to market demands.
Several pivotal quality improvement tools exist to streamline various processes. Six Sigma, for instance, is a robust methodology designed to minimize variability and enhance consistency throughout processes. Lean Management complements this by emphasizing the reduction of waste, promoting efficiency without compromising productivity. The PDCA Cycle offers a structured approach to continuous improvement, while Kaizen fosters a culture of ongoing enhancement across all organizational levels. Understanding and applying these techniques can lead to transformative changes, allowing businesses to thrive in a competitive environment.
Key Quality Improvement Tools for Process Optimization
Quality Improvement Tools are essential for streamlining processes and enhancing operational efficiency. Various methodologies serve distinct purposes, each contributing uniquely to organizational excellence. For instance, Six Sigma focuses on reducing variability, thereby improving the consistency of business processes. This systematic method targets defects and aims for near perfection in output.
Lean Management complements Six Sigma by emphasizing waste reduction while maintaining productivity levels. It fosters a culture of continuous improvement, aligning with the PDCA Cycle, which advocates for planning, doing, checking, and acting on feedback. Additionally, the Kaizen philosophy encourages participation from all employees, transforming incremental changes into significant improvements. Together, these Quality Improvement Tools create a robust framework for achieving heightened quality and optimized processes. Implementing these tools allows organizations to adapt seamlessly to ever-evolving market demands.
insight7: A Leading Solution for Quality Improvement
Insight7 provides organizations with a robust platform designed to enhance quality improvement through improved data analysis capabilities. Companies today are inundated with valuable customer insights gathered from various interactions. However, traditional methods often struggle to keep pace, making it challenging for these organizations to transform raw data into actionable strategies. Insight7 addresses this gap by offering tools that simplify the analysis of customer conversations, enabling quicker responses to insights.
To fully harness the potential of quality improvement tools, Insight7 emphasizes a streamlined, self-service experience. This allows teams to focus on the strategic application of insights rather than getting bogged down in time-consuming data analysis. By enabling organizations to act swiftly, Insight7 positions them ahead of their competition, ensuring that they can effectively translate insights into meaningful business actions and foster a culture of continuous improvement.
insight7 stands out as a versatile tool that allows organizations to streamline processes, gain insights, and implement changes effectively to boost overall quality.
insight7 offers a powerful solution for quality improvement by enabling organizations to refine their processes and gain critical insights. With its user-friendly interface, insight7 helps bridge the gap between data collection and actionable insights, allowing teams to swiftly implement necessary changes. This adaptability makes it an invaluable asset in today’s competitive environment, where the timely application of insights can lead to significant advancements in quality.
By streamlining workflows, insight7 alleviates the challenges posed by traditional analysis methods, which often result in scattered information and inefficiencies. Organizations can gather, analyze, and translate customer feedback directly into business strategies, enhancing collaboration and reducing the time needed for decision-making. These quality improvement tools not only foster a data-driven culture but also empower teams to respond proactively to customer needs, ultimately driving higher quality outcomes.
Other Effective Quality Improvement Tools
Quality Improvement Tools extend beyond the basics and encompass various methodologies that can significantly enhance an organization’s performance. Among these tools, Six Sigma stands out for its rigorous approach to minimizing defects and ensuring consistency across processes. This structured methodology focuses on data analysis and problem-solving, yielding impressive results when reducing variability in production and service delivery.
Another valuable tool is Lean Management, which emphasizes creating more value with fewer resources. By systematically identifying and eliminating waste, organizations can boost productivity while maintaining high-quality standards. Additionally, the PDCA Cycle promotes a culture of continuous improvement, encouraging teams to plan, execute, check, and act on their results. Lastly, adopting Kaizen philosophy fosters a collaborative atmosphere where every employee contributes to ongoing enhancements, solidifying a commitment to quality at all levels. Collectively, these tools underpin a robust framework for effective quality process improvement.
- Six Sigma: A powerful methodology focused on reducing variability and improving process consistency.
Six Sigma is a powerful methodology that aims to significantly reduce variability in processes and enhance consistency. By systematically identifying defects and their root causes, organizations can effectively minimize errors and improve performance. This structured approach, which relies on data-driven decision-making, facilitates informed choices that continuously optimize quality.
To implement Six Sigma effectively, organizations follow several key principles. First, the Define phase outlines project objectives and customer expectations. Next, during the Measure phase, data is collected, revealing current process performance. The Analyze phase identifies root causes of defects, while the Improve phase focuses on developing solutions. Finally, the Control phase ensures that the enhancements are sustained over time.
Adopting Six Sigma as part of your quality improvement tools can lead to measurable gains in efficiency and customer satisfaction, ultimately driving long-term success for your organization.
- Lean Management: A systematic approach to minimizing waste without sacrificing productivity.
Lean Management focuses on refining processes by eliminating waste and enhancing value delivery without compromising productivity. By systematically identifying inefficiencies, organizations can streamline operations and foster innovation. This approach allows for a more responsive environment, ensuring that every action aligns with customer needs.
To effectively implement Lean Management, organizations can consider several key strategies:
Value Stream Mapping: Visualize the flow of materials and information to identify bottlenecks and improve efficiency.
Continuous Improvement (Kaizen): Encourage all employees to contribute ideas for process enhancements, leading to incremental gains over time.
Just-In-Time Production: Align production schedules closely with customer demand to minimize excess inventory and reduce waste.
5S Methodology: Utilize Sort, Set in order, Shine, Standardize, and Sustain to create and maintain an organized workspace.
Through these tools and techniques, Lean Management empowers organizations to enhance their quality improvement processes, ultimately achieving superior results and sustained competitive advantages.
- PDCA Cycle (Plan-Do-Check-Act): An iterative method for controlling and continuous improvement of processes and products.
The PDCA Cycle, an iterative method known as Plan-Do-Check-Act, serves as a fundamental framework for effective quality improvement. This approach emphasizes the importance of planning for improvements, executing those plans, and then checking or evaluating the results. By iterating through these steps, organizations can promote consistent advancements in their processes and products.
In practicing the PDCA Cycle, the first step involves planning by identifying specific goals and outlining measurable objectives. Next, in the “Do” phase, the plans are implemented to test their efficacy. Following this, the “Check” phase occurs, where the results are analyzed to determine if the expected outcomes were achieved. Finally, the “Act” phase involves making necessary adjustments based on the analysis before repeating the cycle. This continuous loop not only enhances efficiency but also integrates quality improvement tools into decision-making processes.
- Kaizen: A philosophy that emphasizes ongoing improvement and involves all employees from CEOs to assembly line workers.
Kaizen is a transformative philosophy that hinges on the belief that small, continuous improvements lead to significant advancements over time. It promotes the involvement of every employee, from the CEO to the assembly line worker, fostering a culture where everyone's input is valued. This collective effort empowers employees to identify inefficiencies and suggest improvements in their daily tasks, ultimately enhancing overall quality.
The essence of Kaizen is to create a work environment that nurtures open communication and teamwork. Implementing this philosophy means embracing various quality improvement tools that facilitate ongoing evaluations and enhancements. For instance, regular team meetings can be held to discuss progress and brainstorm solutions. Additionally, training sessions ensure that all employees understand the tools at their disposal, allowing them to contribute meaningfully to the quality improvement process. By embedding Kaizen into daily operations, organizations cultivate a sustainable model of excellence.
Steps for Implementing Quality Improvement ProcessesExtract insights from interviews, calls, surveys
and reviews for insights in minutes
Extract insights from interviews, calls, surveys and reviews for insights in minutes
Implementing quality improvement processes involves a structured approach that enhances operational effectiveness. Begin by identifying the specific areas in need of improvement through careful analysis and data evaluation. This initial step aligns with the broader objectives of utilizing quality improvement tools to drive sustainable enhancements. By understanding current challenges, organizations can ensure a focused approach to quality advancements.
Next, deploy the right quality improvement tools tailored to your unique requirements. Whether opting for Six Sigma, Lean Management, or the PDCA Cycle, selecting suitable methodologies is crucial in addressing the identified issues effectively. This strategic choice not only optimizes quality processes but also builds a foundation for ongoing monitoring and adjustments. Finally, establish a culture of continuous improvement by regularly analyzing outcomes and fine-tuning processes based on feedback and results. This iterative process is vital for nurturing a quality-centered organization.
Step 1: Identification and Analysis of Areas Needing Improvement
Identification and analysis of areas needing improvement is a foundational step in initiating effective quality improvement efforts. This phase requires a thorough examination of processes, outcomes, and employee feedback to reveal weaknesses. Organizations can use various quality improvement tools to gather and analyze data, identify trends, and pinpoint issues that hinder performance. Understanding the underlying causes of these challenges is essential for effective problem resolution.
During this stage, quantitative metrics and qualitative insights play a crucial role. Analyzing customer feedback, performance reports, and operational data provides a more comprehensive view of where improvements are needed. Utilizing tools such as root cause analysis or process mapping can help visualize interactions and dependencies, enabling teams to systematically address inefficiencies. By accurately identifying and analyzing areas needing improvement, organizations lay the groundwork for implementing targeted interventions and ultimately enhancing overall quality.
Pinpoint areas that require enhancements by conducting comprehensive assessments and using data-driven insights.
Identifying areas that need improvement is crucial for fostering a culture of quality within an organization. Comprehensive assessments should be the starting point; they provide a holistic view of existing processes and pinpoint inefficiencies. Gathering data-driven insights allows teams to uncover patterns and trends within their operations. By analyzing this information, organizations can make informed decisions on where enhancements are necessary, ensuring that resources are allocated effectively and strategically.
Quality improvement tools play an essential role in this process. Techniques such as Six Sigma, Lean Management, and the PDCA cycle help structure the assessment phase. Implementing a systematic approach encourages continual evaluation and improvement, ultimately leading to greater operational efficiency and enhanced quality. This iterative cycle promotes a proactive stance on quality, enabling organizations to adapt and thrive in a dynamic environment.
Step 2: Deploying the Right Quality Improvement Tools
Selecting the appropriate quality improvement tools is vital for turning insights into actionable results. The right tools can help organizations effectively tackle identified issues and streamline processes. It's essential to match the tools with specific needs, ensuring that they align well with the organization’s goals and the challenges at hand. Consider using methodologies like Six Sigma or Lean Management, which focus on reducing waste and enhancing quality across various functions.
To deploy the right quality improvement tools successfully, follow these steps:
- Assess Requirements: Identify specific needs through thorough analysis and discussions with stakeholders.
- Match Tools to Needs: Choose tools that offer features and methodologies best aligned with identified areas for improvement.
- Train Teams: Equip team members with the necessary training to maximize the effectiveness of the selected tools.
- Implement Gradually: Start with pilot projects to test the tools' effectiveness before a full-scale rollout.
- Evaluate Results: After implementation, constantly assess the outcomes and make adjustments as needed.
By systematically following these steps, organizations can leverage quality improvement tools to enhance processes effectively and promote continuous improvement.
Choose and employ the tools best suited to your specific needs to address the identified areas effectively.
Choosing the right quality improvement tools is essential for addressing specific challenges effectively. It begins with a thorough evaluation of the issues at hand. Understand the nuances of each problem, as this clarity will guide you to select suitable methodologies or systems. Whether it's Lean Management to eliminate waste or Six Sigma to reduce variability, knowing your objectives is crucial in making informed decisions.
Once the correct tools are selected, it’s vital to implement them strategically. Engage with your team to ensure everyone understands how these tools align with organizational goals. Continuous feedback and data analysis allow for real-time adjustments, ensuring improvements are effective and measurable. By maintaining an agile approach, you create a work environment that continually evolves, enhancing quality over time. Ultimately, adopting quality improvement tools tailored to your specific needs will empower your organization to thrive in a competitive landscape.
Step 3: Monitoring and Fine-tuning Processes
Monitoring and fine-tuning processes is a pivotal stage in the journey of quality improvement. It involves the continuous evaluation of implemented changes to ensure they are producing the desired outcomes. Quality improvement tools play an essential role here, allowing teams to collect data, analyze results, and identify any discrepancies. This ensures that every adjustment aligns with the overarching goals of enhancing efficiency and effectiveness.
As organizations implement new strategies, ongoing assessment becomes crucial. Key factors to monitor include performance metrics, employee feedback, and customer satisfaction. Regularly reviewing these elements helps identify areas that need further attention or modification. By adopting a proactive approach to monitoring, organizations can swiftly adapt to challenges and pivot their strategies accordingly. This ongoing process of fine-tuning reinforces a culture of continuous improvement, making it easier to achieve long-term quality enhancements. Through diligent monitoring and adjustment, businesses can maintain a competitive edge and better serve their customers.
Continuously monitor the outcomes, making necessary adjustments and improvements as part of an adaptive process.
Monitoring outcomes consistently is crucial for effective quality improvement. By regularly assessing the results of implemented changes, organizations can identify areas for enhancement. This adaptive monitoring process ensures that strategies align with organizational goals, leading to sustained growth. Utilizing quality improvement tools can facilitate this assessment, allowing teams to track performance metrics efficiently.
Making necessary adjustments requires a willingness to adapt. Organizations should encourage feedback loops where insights from employees and customers are actively solicited. These insights can illuminate issues that may not be immediately obvious. Integrating adjustments based on data-driven decision-making supports continuous improvement. Ultimately, this iterative approach promotes a culture of excellence, fostering an environment where all stakeholders contribute to enhancing quality outcomes. By embracing this adaptive process, organizations can ensure they remain competitive and responsive to evolving market needs.
Conclusion on Quality Improvement Tools
Quality improvement tools play a pivotal role in enhancing operational efficiency and effectiveness within organizations. These tools, such as Six Sigma and Lean Management, provide frameworks for identifying inefficiencies and fostering continuous improvement. When properly applied, they help streamline processes and elevate the overall quality of products and services offered.
The journey of quality improvement requires commitment and a systematic approach. By integrating these tools into daily operations, organizations can not only address current challenges but also prepare for future demands. Ultimately, the right quality improvement tools will empower teams to achieve sustainable growth and drive excellence in every aspect of their work.
Quality improvement is an ongoing journey, and having the right tools and methodologies in place is critical. By understanding and leveraging effective quality improvement tools, organizations can achieve significant advancements in their processes, leading to better outcomes, increased efficiency, and sustainable success.
Quality improvement is an ongoing journey that requires consistent effort and the right set of tools and methodologies. Organizations can significantly enhance their processes by adopting effective quality improvement tools that not only streamline operations but also lead to improved outcomes. This approach emphasizes the need for continuous assessment and adjustment, ensuring a dynamic process that evolves with changing demands and challenges.
Key quality improvement tools facilitate this journey by addressing various aspects of process optimization. For instance, Six Sigma targets process variability to enhance consistency, while Lean Management focuses on minimizing waste to boost productivity. The PDCA Cycle encourages a systematic approach to refining processes, and Kaizen promotes a culture of continuous improvement involving all team members. By implementing these methodologies and understanding their functionalities, entities can foster a sustainable path toward success and operational excellence.