Best 10 Manufacturing Process Analysis Tools
-
Bella Williams
- 10 min read
Top Manufacturing Tools serve as integral components in modern manufacturing processes, facilitating efficient analysis and continuous improvement. Organizations today face immense pressure to optimize operations, reduce waste, and enhance productivity. By leveraging these tools, manufacturers can gain valuable insights that drive strategic decision-making and enhance overall performance.
As we delve into the realm of manufacturing process analysis, it becomes essential to understand what features distinguish effective tools. The best manufacturing tools not only simplify data collection and visualization but also support collaboration among team members. By identifying the right tools, companies can create tailored solutions that significantly impact their manufacturing outcomes and ensure they remain competitive in a rapidly evolving industry.
Analyze & Evaluate Calls. At Scale.
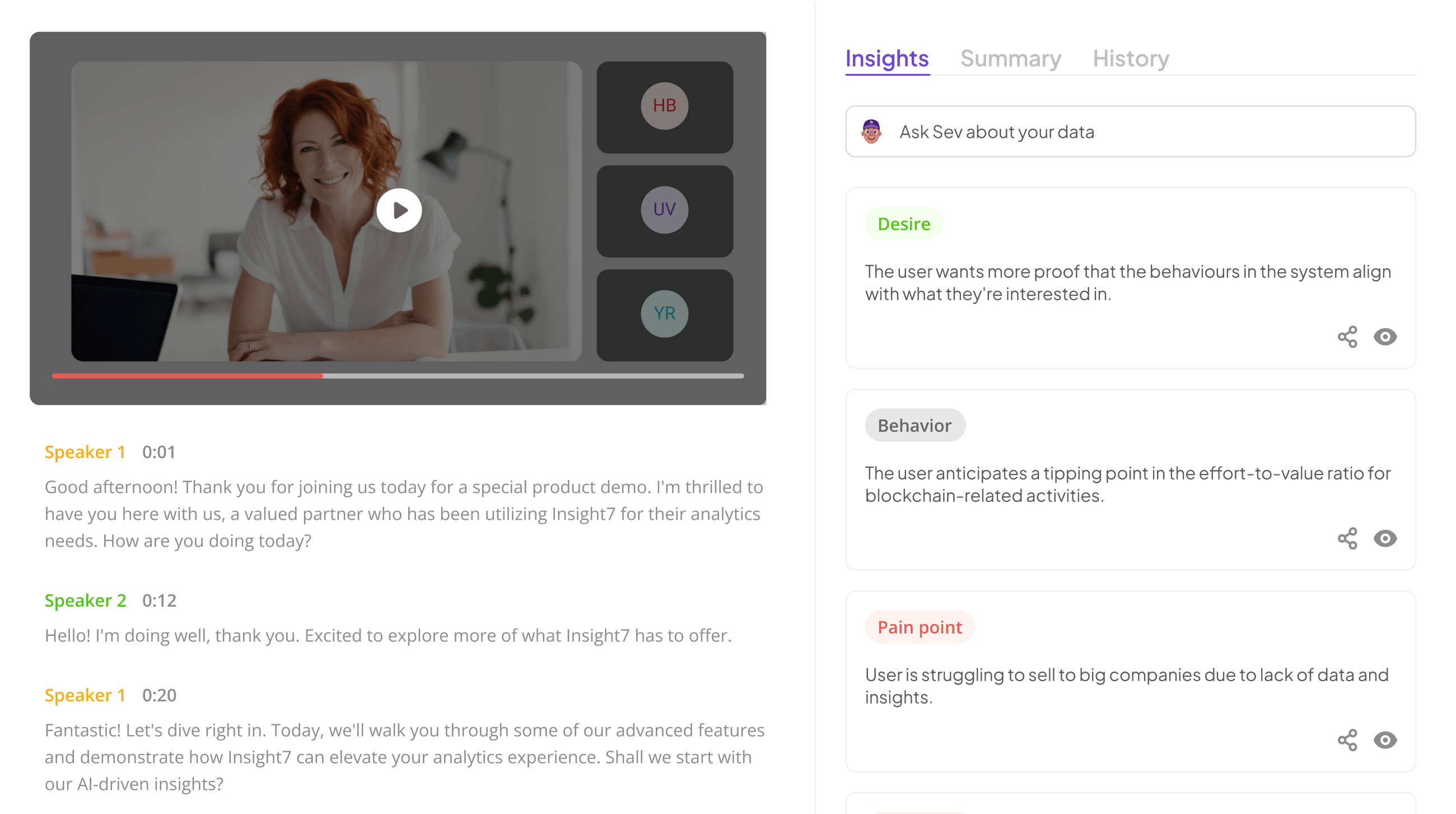
Understanding the Importance of Top Manufacturing Tools
Top Manufacturing Tools play a crucial role in enhancing operational efficiency within the manufacturing sector. Understanding their importance begins with recognizing how these tools facilitate process analysis, leading to improved decision-making and resource management. By streamlining workflows, manufacturers can identify bottlenecks, reduce waste, and ultimately drive productivity. This transformation not only saves time but also enhances the overall quality of production.
Moreover, effective manufacturing tools equip organizations with insights that can shape strategic initiatives. They enable teams to visualize complex processes, collaborate effortlessly, and convert analytical findings into actionable business strategies. For instance, tools that focus on data analysis offer companies a clearer understanding of their operations, allowing for continuous improvement. Thus, prioritizing the use of top manufacturing tools is vital for staying competitive and adapting to evolving market demands. Embracing these tools can lead to sustained success in a challenging industry landscape.
Why Process Analysis Matters in Manufacturing
Process analysis is crucial in manufacturing because it directly impacts efficiency and productivity. By systematically examining production processes, businesses can identify areas that require improvement and eliminate waste. With the help of top manufacturing tools, manufacturers can streamline operations, minimize errors, and enhance product quality.
For instance, consider how tools that analyze workflow can pinpoint bottlenecks in production lines. These insights allow manufacturers to implement changes that enhance speed and efficiency, leading to higher output rates. Moreover, tracking performance metrics through advanced software enables manufacturers to make data-driven decisions, ensuring continual process optimization. Consequently, organizations that prioritize process analysis using the best tools are better positioned to compete in today's fast-paced market.
- The role of process analysis in enhancing efficiency and productivity.
Process analysis plays a crucial role in enhancing efficiency and productivity within the manufacturing sector. By breaking down processes into measurable components, organizations can identify bottlenecks and areas for improvement. This detailed examination leads to streamlined workflows, reducing waste and increasing output. When manufacturers utilize top manufacturing tools, they gain insights that directly contribute to operational excellence, enabling them to focus on critical areas that yield the highest returns.
Implementing effective process analysis tools allows for real-time monitoring and data collection, improving decision-making across the board. For instance, tools that provide detailed visualizations and simulations enable teams to pinpoint inefficiencies before they escalate. Ultimately, the synergy between process analysis and manufacturing tools results in a more agile, responsive production environment, ensuring that companies can adapt to market demands while maintaining high standards of quality and efficiency.
- Examples of how process analysis tools have transformed manufacturing processes.
Process analysis tools have significantly transformed manufacturing processes by enhancing efficiency and driving productivity. For instance, tools like Minitab utilize statistical methods to identify bottlenecks, enabling teams to implement data-driven decisions that improve output quality. Likewise, simulations powered by software such as SIMUL8 allow manufacturers to visualize various scenarios, leading to more informed strategies tailored to specific production challenges.
Another noteworthy example includes Lucidchart, which simplifies process visualization. By offering collaborative features, it enables teams to work together to pinpoint inefficiencies and streamline workflows. Additionally, Microsoft Visio provides advanced diagramming tools that help manufacturers accurately depict complex processes, ensuring everyone has a clear understanding of their roles. Collectively, these top manufacturing tools empower companies to innovate and adapt, fostering an environment where continuous improvement is the norm.
Key Features of Effective Manufacturing Tools
Effective manufacturing tools play a pivotal role in enhancing productivity and quality within manufacturing processes. One key feature of these tools is user accessibility; they should be easy to use, ensuring that every team member can operate them without extensive training. This democratization of access enables organizations to gather insights swiftly, leading to timely adjustments in processes.
Another essential characteristic is data visualization, which allows users to comprehend complex information quickly. This feature aids in identifying pain points and opportunities for improvement. Additionally, integration capabilities are crucial; tools must seamlessly connect with existing systems to ensure a smooth workflow. Furthermore, the best manufacturing tools offer robust analytical functions, enabling teams to extract actionable insights from data collected throughout the manufacturing process. These features collectively contribute to effective decision-making, ultimately driving operational excellence.
In summary, selecting the right top manufacturing tools involves assessing usability, visualization, integration, and analytics. By focusing on these key features, organizations can better align their tools with their operational objectives and enhance overall efficiency.
- Criteria for selecting a manufacturing process analysis tool.
When selecting a manufacturing process analysis tool, several key criteria should be considered to ensure optimal effectiveness. First, assess the tool's compatibility with your existing systems and processes. A tool that integrates seamlessly into your current workflow will save time and resources during implementation. Moreover, user-friendliness is critical; the easier a tool is to use, the more likely it is that staff will engage with it effectively.
Next, evaluate the features offered by the tool. Essential capabilities might include data visualization, real-time analytics, and reporting functionalities. These features not only enhance decision-making but also enable you to monitor performance trends over time. Additionally, consider the tool's scalability to accommodate future growth. The right analysis tool should help facilitate continuous improvement and adapt to changing manufacturing needs. Thus, by carefully considering these criteria, businesses can effectively leverage top manufacturing tools to enhance their operational processes.
- Case studies of successful tool implementation.
Implementing manufacturing process analysis tools can significantly enhance operational efficiency and quality control. Case studies illustrate how companies have effectively utilized these top manufacturing tools to streamline their processes. For instance, one organization adopted a statistical analysis tool to identify bottlenecks in production. This initiative led to a remarkable 25% increase in throughput by reengineering their workflow in response to the data gathered.
Another example involved leveraging simulation tools to visualize and optimize manufacturing lines. By modeling various scenarios, the organization was able to make informed decisions, resulting in reduced lead times and cost savings. These successful stories highlight the importance of selecting the right tools that align with strategic goals. Moreover, they demonstrate that when properly implemented, top manufacturing tools can catalyze transformation and ensure sustained competitive advantage in the industry.
Extract insights from interviews, calls, surveys and reviews for insights in minutes
Top Manufacturing Tools: Leading Options for Process Analysis
Top Manufacturing Tools are essential for effectively analyzing processes and driving improvement in manufacturing environments. Various tools offer unique features that cater to specific needs, ensuring streamlined operations. This section highlights some leading options for process analysis, showcasing their capabilities and benefits.
Among the top tools, Minitab excels with its robust statistical analysis features, enabling manufacturers to make data-driven decisions. SIMUL8 stands out for its simulation capabilities, allowing users to visualize and optimize processes. Lucidchart simplifies process mapping through intuitive design elements, promoting team collaboration. Additionally, Microsoft Visio provides advanced diagramming tools that enhance clarity in process layout.
These tools equip manufacturers with the insights needed to enhance productivity, reduce waste, and foster continuous improvement. By adopting suitable analysis tools, organizations can navigate the complexities of manufacturing with confidence and precision.
Insight7: The Game-Changer in Manufacturing Analysis
In the landscape of manufacturing analysis, game-changing tools are revolutionizing the way organizations optimize their processes. Insight7 stands out by offering a self-service platform that simplifies the analysis of vast amounts of data. Businesses today are inundated with customer signals, making it increasingly difficult to extract actionable insights using traditional methods. With Insight7, users can efficiently analyze customer conversations, aligning insights with strategic objectives.
Furthermore, the platform addresses common pain points associated with manual analysis, such as inefficiencies in collaboration and slow delivery timelines. By streamlining the process, companies can quickly turn insights into actions. Overall, the adaptability and innovation of Insight7 illustrate how the top manufacturing tools are not just enhancements, but essential components for staying competitive in the modern market. Embracing this technology could be the key to achieving operational excellence.
- Overview of features and benefits.
In exploring the top manufacturing tools, it is essential to understand their features and benefits. These tools enhance operational efficiency by providing in-depth analysis and insights into manufacturing processes. They can help identify bottlenecks, reduce waste, and optimize resource allocation, which ultimately leads to cost savings and improved productivity.
The features of these tools typically include advanced analytics capabilities, user-friendly interfaces, and integration with existing systems. For instance, statistical tools like Minitab facilitate data-driven decision-making, while simulation software such as SIMUL8 can visualize process flows for better understanding. Additionally, collaboration features in tools like Lucidchart and Microsoft Visio streamline team efforts, ensuring everyone is aligned on process improvements. Adopting these tools not only boosts manufacturing efficacy but also cultivates a culture of continuous improvement across operations.
- How Insight7 streamlines manufacturing processes.
Streamlining manufacturing processes is vital for maintaining competitiveness in today's fast-paced environment. By utilizing effective analysis tools, businesses can gain better insights into their operations, driving improvements in efficiency and productivity. A notable tool that excels in this area enables companies to rapidly analyze large volumes of customer data and feedback, transforming raw information into actionable insights that inform strategic decisions.
One of the standout features of this tool is its user-friendly interface, which allows teams to effortlessly access and interpret data from customer interactions. This not only accelerates the decision-making process but also enhances collaboration among different departments by centralizing information storage. Moreover, manufacturers can adapt quickly to changing market demands by harnessing data-driven insights, ultimately leading to more agile and responsive operations. These benefits illustrate how leveraging top manufacturing tools can lead to significant improvements in overall performance and competitiveness.
Other Noteworthy Tools for Manufacturing Process Analysis
Manufacturers continuously seek effective methods to enhance their efficiency and productivity. Beyond the commonly recognized tools, there are several other noteworthy solutions for manufacturing process analysis that cater to various needs. One such tool is Minitab, which offers advanced statistical analysis features. This software is particularly beneficial for organizations aiming to perform in-depth process improvement assessments and integrate seamlessly with existing systems.
Another notable tool is SIMUL8, which excels in simulating processes to visualize potential outcomes before implementation. This capability allows teams to map out various scenarios and test efficiencies without affecting production directly. Additionally, Lucidchart serves as an excellent platform for simplifying process visualization, promoting collaboration among teams. Microsoft Visio also deserves mention for its robust diagramming capabilities, ensuring clear documentation of process layouts. Together, these tools complement the top manufacturing tools, providing diverse functionalities to enhance process analysis.
Tool 1: Minitab
Minitab stands out as one of the top manufacturing tools for process analysis, offering a comprehensive suite of statistical tools designed for process improvement. Its user-friendly interface makes data analysis accessible, even to those with limited statistical knowledge. Users can leverage features such as control charts, ANOVA, and regression analysis to identify areas for improvement and make data-driven decisions.
Integration with other systems can enhance Minitab's functionality, allowing companies to conduct in-depth analyses without disrupting existing workflows. The software also facilitates visualization of complex data, making it easier for teams to interpret results and communicate findings. Minitab's capabilities not only streamline manufacturing processes but also empower teams to foster a culture of continuous improvement. By embracing tools like Minitab, manufacturers can significantly enhance productivity and efficiency across their operations, ultimately driving better outcomes.
- Statistical tools for process improvement.
Statistical tools play a crucial role in process improvement within manufacturing. These tools allow organizations to analyze data effectively, leading to enhanced efficiency and productivity. Utilizing statistical methods can help identify patterns, measure performance, and uncover insights that drive informed decision-making. For example, statistical process control charts facilitate real-time monitoring of processes, allowing manufacturers to address deviations promptly and reduce waste.
When considering the top manufacturing tools, it is essential to evaluate their statistical capabilities. Key statistical tools include Minitab, which offers comprehensive data analysis options, and SIMUL8, which provides simulation techniques for process optimization. These tools help manufacturers implement systematic approaches to problem-solving, resulting in measurable improvements. By integrating such statistical tools into their operations, organizations can sustain competitive advantages and foster continuous improvement in their processes.
- Usability and integration with existing systems.
Usability and integration with existing systems are crucial factors when considering the Top Manufacturing Tools. A tool's interface should be intuitive, allowing users across various departments to operate it without extensive training. This democratization of insights enables team members to engage actively with the data, enhancing collaboration and efficiency.
Integration with existing systems is equally vital. The tool should seamlessly connect with current workflows, databases, and software applications to ensure a smooth transition and minimize disruption. This compatibility is particularly important when extracting and analyzing data across multiple platforms. By facilitating easy data sharing and communication, organizations can leverage the full potential of their manufacturing process analysis to drive continuous improvement. Ultimately, usability and integration empower teams to make informed decisions, optimize processes, and achieve greater productivity in their manufacturing efforts.
Tool 2: SIMUL8
SIMUL8 is a powerful simulation software that plays a critical role in analyzing manufacturing processes. This tool allows users to visualize process flows, identify bottlenecks, and estimate resource utilization effectively. By simulating various scenarios, businesses can predict outcomes and make informed decisions that streamline operations and increase efficiency.
One of the standout features of SIMUL8 is its user-friendly interface. Users can create detailed process maps quickly, setting parameters for different stages of production. Additionally, the software offers data analysis capabilities that support real-time decision-making. Many companies have successfully transformed their operations by employing SIMUL8, leading to reduced lead times and optimized workflows. As businesses strive to enhance their competitiveness, tools like SIMUL8 become essential in the toolkit of top manufacturing tools, aiding in strategic planning and operational improvements.
- Benefits of simulation in process mapping.
Simulation plays a crucial role in process mapping by allowing manufacturers to visualize and evaluate their workflows. When using top manufacturing tools, simulation helps identify bottlenecks and inefficiencies before real-world implementation. This proactive approach not only saves time but also minimizes the risk of costly errors that might occur during actual operations.
One of the primary benefits of simulation is enhanced decision-making. By evaluating multiple scenarios virtually, organizations can assess the potential impact of changes on overall productivity and resource utilization. Furthermore, simulation enables teams to assess various training approaches, ensuring that employees are well-prepared for changes in the production process. Ultimately, incorporating simulation in process mapping empowers manufacturers to streamline operations and drive continuous improvement in their workflows.
- Scenarios and case applications.
In analyzing the adoption of top manufacturing tools, various scenarios and case applications reveal their effectiveness across diverse settings. For example, a company focused on quality assurance implemented a statistical analysis tool, significantly reducing defects over a six-month period. This success story illustrates how utilizing the right manufacturing tools can enhance product quality and streamline processes.
Another scenario involves a team using simulation software to map complex workflows. By visualizing potential bottlenecks, they optimized their production line, resulting in a notable reduction of cycle time. Such applications highlight the versatility of manufacturing process analysis tools in addressing specific operational challenges. As organizations continue to seek improvements, examining these real-world cases provides insights into best practices and the transformative power of effective analysis tools.
Tool 3: Lucidchart
Lucidchart stands out among the top manufacturing tools by providing a streamlined approach to process visualization. Users can create flowcharts, diagrams, and organizational charts easily, making complex processes easier to grasp and share. With its intuitive interface, training is minimal, allowing teams to focus on improving efficiency rather than learning the tool itself.
Moreover, Lucidchart's collaboration features enhance teamwork. Multiple users can work on diagrams simultaneously, enabling real-time feedback and adjustments. This capability fosters a dynamic environment where insights can be quickly translated into actionable changes in the manufacturing process. By integrating with other applications, Lucidchart simplifies data sharing and enhances overall workflow, making it an essential tool for organizations aiming to boost productivity and streamline operations.
- Simplifying process visualization.
Visualizing a manufacturing process can significantly enhance understanding and decision-making. Simplifying process visualization helps in breaking down complex workflows into easily digestible visual formats. This transforms abstract data into meaningful insights, allowing teams to identify bottlenecks and inefficiencies swiftly. By employing the right tools, manufacturers can depict processes in a way that highlights critical areas requiring improvement.
In the realm of top manufacturing tools, visual aids such as flowcharts, diagrams, and simulations become essential. Utilizing platforms like Lucidchart and Microsoft Visio enables teams to collaborate and create process maps that are clear and informative. These visualizations not only foster better communication among team members but also facilitate effective training of new employees. Ultimately, simplifying process visualization empowers manufacturers to adapt swiftly, innovate effectively, and maintain a competitive edge.
- Collaboration features for team-based analysis.
Collaboration features are crucial for team-based analysis in manufacturing. These tools facilitate communication, allowing teams to work together effectively, even when distances separate them. By enabling real-time sharing of insights and data, manufacturing teams can collaboratively tackle complex problems. The integration of features such as shared workspaces, comment sections, and version history ensures everyone stays aligned and informed throughout the analysis process.
One essential aspect of effective collaboration is the ability to visualize data collectively. Tools like Lucidchart and Microsoft Visio offer intuitive visual aids that enable teams to map out processes and identify bottlenecks together. Additionally, workflow management features allow for task assignments and deadlines, ensuring that everyone contributes to a common goal. Overall, leveraging robust collaboration features within top manufacturing tools fosters a productive environment where insights can be transformed into actionable strategies, ultimately enhancing the efficiency of manufacturing processes.
Tool 4: Microsoft Visio
Microsoft Visio plays a pivotal role in the realm of manufacturing process analysis, particularly when it comes to visual representation. This tool is renowned for its advanced diagramming capabilities, allowing users to create detailed flowcharts and process maps. By effectively visualizing processes, manufacturers can identify bottlenecks and inefficiencies. This aids in streamlining operations and understanding workflow dynamics.
Its versatility makes Visio applicable across various industries, from automotive to electronics. Users can customize diagrams, ensuring that the layout reflects their specific process needs. Moreover, Visio integrates seamlessly with other software systems, enhancing collaboration among team members. The intuitive interface facilitates easy adoption for users, making it one of the top manufacturing tools available. By harnessing Microsoft Visio, organizations can improve their process analysis, ultimately leading to increased efficiency and productivity in their manufacturing practices.
- Advanced diagramming tools for process layout.
Advanced diagramming tools play a critical role in process layout, offering businesses a visual representation of workflows. These tools enable teams to create detailed diagrams that illustrate the various steps involved in manufacturing, thereby facilitating better understanding and communication. When utilized effectively, advanced diagramming tools help identify inefficiencies and optimize processes, leading to increased productivity and reduced waste.
Among the most popular options are Microsoft Visio and Lucidchart, which provide customizable templates and intuitive interfaces for diagram creation. These tools allow users to map out process flows, identify bottlenecks, and highlight opportunities for improvement. By visualizing information, teams can engage in collaborative discussions, ensuring that everyone is on the same page. As part of the broader context of Top Manufacturing Tools, these advanced diagramming solutions serve as foundational elements in successful process analysis and continuous improvement strategies.
- Industry applications and ease of use.
Industry applications for manufacturing process analysis tools are diverse and impactful. These tools find utility across various sectors, including automotive, pharmaceuticals, and electronics. By employing top manufacturing tools, companies can streamline operations, reduce waste, and enhance productivity. Furthermore, tools like Minitab and SIMUL8 empower manufacturers to understand data deeply and simulate process changes, offering a clear pathway for improvement.
Ease of use is equally vital for successful implementation. User-friendly interfaces and intuitive dashboards ensure that teams can quickly adapt to these tools without extensive training. For instance, collaboration features in Lucidchart allow teams to visualize processes collectively, emphasizing teamwork. Effective integration of these tools can transform manufacturing workflows, making processes more transparent and manageable. Ultimately, the right tools can significantly contribute to an organizationโs efficiency and adaptability, reflecting a shift towards data-driven decision-making in the manufacturing landscape.
Steps to Implement Manufacturing Process Analysis Tools
To successfully implement manufacturing process analysis tools, the first step is to define clear objectives and requirements. This involves identifying what you aim to achieve through these tools, such as improving efficiency, reducing waste, or enhancing quality control. By establishing specific goals, you can tailor your tool selection to meet the unique needs of your manufacturing environment.
The next step is to carefully select and integrate your chosen tools into your workflow. Evaluate candidate tools based on their compatibility with existing processes and features that align with your goals. Once selected, ensure a seamless integration by training your team and allowing time for adjustments. Following these steps will prepare your organization for successful adoption of the top manufacturing tools, maximizing their potential for process improvement and fostering a culture of continuous enhancement.
Step 1: Define Objectives and Requirements
To create an effective manufacturing process analysis, the first step is to define clear objectives and requirements. This foundational stage guides the selection of the top manufacturing tools suited for your specific needs. Start by identifying what you aim to achieve through the tool, whether itโs improving efficiency, reducing waste, or enhancing quality control. Clearly stated goals help stakeholders understand the purpose behind the tool selection, setting the stage for successful implementation.
Additionally, assess the unique requirements of your manufacturing environment. Each process is different, necessitating tools that can adapt to specific workflows and compliance standards. Collect input from team members and decision-makers to create a comprehensive list of features desired. By aligning objectives and requirements, organizations can effectively streamline their selection process, ensuring that the chosen tools genuinely fit their operational landscape and elevate overall productivity.
- Identifying the goals behind using the tools.
To effectively realize the benefits offered by the top manufacturing tools, organizations must clearly define their goals. Understanding the objectives behind utilizing these tools is crucial in optimizing manufacturing processes. Common goals include enhancing productivity, reducing waste, and improving quality control. Each of these objectives requires a specific focus during the selection and application of manufacturing analysis tools.
Additionally, aligning these tools with business goals enables companies to tailor their strategies for maximum efficiency. For instance, if the objective is to reduce cycle times, a simulation tool may be prioritized over others. Itโs essential to communicate these goals to all stakeholders, ensuring everyone understands how the selected tools will contribute to the overall manufacturing strategy. By identifying and articulating these goals, organizations can effectively choose the right tools and implement them successfully to transform their manufacturing processes.
- Tailoring tools to specific manufacturing needs.
Choosing the right manufacturing process analysis tool is crucial for meeting specific operational needs. Tailoring tools to these needs ensures that manufacturers can optimize efficiencies and enhance productivity. Each manufacturing environment is unique, necessitating an assessment of objectives and challenges before deploying any tool. Considerations might include production scale, complexity of processes, and available resources.
Several key factors should guide the customization of manufacturing tools. First, engage stakeholders to identify critical pain points in current processes. Secondly, evaluate whether tools can be integrated seamlessly into existing workflows. Lastly, prioritize user-friendliness to promote team adoption. By aligning tool features with specific manufacturing requirements, organizations can maximize the benefits of top manufacturing tools and achieve sustained operational excellence.
Step 2: Select and Integrate Tools in Workflow
In the quest to improve manufacturing efficiency, selecting and integrating the right tools is crucial. Begin by identifying your specific objectives, as these will guide you in evaluating various options. Focus on the features that align with your operational needs, such as data analysis capabilities or ease of team collaboration. The right tools can significantly enhance your workflow, turning raw data into actionable insights.
Once you have selected the top manufacturing tools, consider how they will fit into existing processes. Itโs vital to ensure that integration is seamless to minimize disruption. Training team members on the new tools is also essential for maximizing their potential. By effectively integrating these tools, you empower your team to make data-driven decisions that improve processes and outcomes, leading to a more efficient manufacturing environment.
- Guidelines for tool selection.
Selecting the right process analysis tools is crucial for enhancing manufacturing efficiency. Focus on a few key criteria to ensure effective decision-making. Start by evaluating the specific needs of your organization. Understanding your processes, objectives, and constraints is essential in aligning the selected tools with your operational goals.
Next, consider the integration capabilities of the tools. They should seamlessly fit into your existing processes and systems to minimize disruptions. Another important factor is user-friendliness; tools that are straightforward and intuitive facilitate quicker adoption among team members. Additionally, assess the support and training provided by the vendors, as this will greatly influence the implementation success.
When selecting among the top manufacturing tools, always aim for solutions tailored to your specific operational goals. By following these guidelines, you can enhance your organization's analytical capabilities and ultimately drive better outcomes in manufacturing processes.
- Ensuring smooth integration into existing processes.
To ensure smooth integration of top manufacturing tools into existing processes, organizations need to focus on a structured approach. Initially, aligning the new tools with current workflows is essential. This means identifying how these tools can complement existing systems and practices, thereby enhancing efficiency without causing disruptions.
Next, itโs crucial to engage all stakeholders throughout the integration process. Communication helps address resistance and fosters a collaborative environment. Providing adequate training on the new tools ensures that employees are equipped to utilize the features effectively. Keeping feedback channels open allows for continuous improvement, enabling refinements based on user experience.
Ultimately, the goal is to create an environment where technology and process flow seamlessly together, enhancing not just productivity but also maintaining a positive workforce morale during the transition. Following these steps will lead to a successful implementation of the most effective manufacturing process analysis tools.
Conclusion: Leveraging Top Manufacturing Tools for Continued Success
To ensure continued success in manufacturing, utilizing top manufacturing tools is essential. These tools not only streamline processes but also enhance productivity by providing valuable insights. When effectively implemented, they can lead to significant improvements in operational efficiency and decision-making capabilities.
Manufacturers that embrace these tools can stay ahead of the competition by quickly responding to market demands and optimizing their resources. By focusing on analysis and collaboration, organizations can transform their processes and drive sustained growth. Emphasizing continuous improvement through data-driven strategies will ultimately secure long-term success in the ever-evolving manufacturing landscape.