5 Common Errors in QA Calibration Sessions
-
Bella Williams
- 10 min read
Understanding the intricacies of calibration mistakes analysis in QA sessions is essential for maintaining product excellence. Calibration sessions aim to ensure consistent quality across evaluations, yet common errors can undermine these goals. Identifying these pitfalls is the first step towards enhancing the calibration process, promoting alignment among team members and improving overall productivity.
In this section, we will dissect prevalent errors that often occur during QA calibration, shedding light on their causes and impacts. By recognizing these mistakes, organizations can implement targeted strategies to correct them and avoid similar issues in the future, ultimately leading to a more effective quality assurance system.
Understanding and addressing common errors in Quality Assurance (QA) calibration sessions is crucial for maintaining high standards in product quality. In this blog post, well delve into the Calibration Mistakes Analysis of these sessions to uncover prevalent errors and offer solutions.
Effectively understanding and addressing common errors in Quality Assurance (QA) calibration sessions is essential for maintaining high standards in product quality. One of the critical aspects of this process is Calibration Mistakes Analysis, which helps illuminate prevalent errors that can arise during these sessions. By pinpointing these mistakes, teams can develop targeted strategies to enhance the calibration process, ensuring more consistent and reliable outcomes.
One significant error often encountered is the misalignment of quality standards among team members. When each person has a different interpretation of what constitutes quality, inconsistency in evaluations can occur. Regular team meetings can help align expectations and reinforce a unified definition of quality. Additionally, inadequate training or lack of appropriate tools can lead to calibration errors. Investing in comprehensive training and utilizing effective tools—such as Insight7 and Qualityze—can significantly improve the accuracy of QA assessments, fostering a culture of continuous improvement.
Analyze & Evaluate Calls. At Scale.
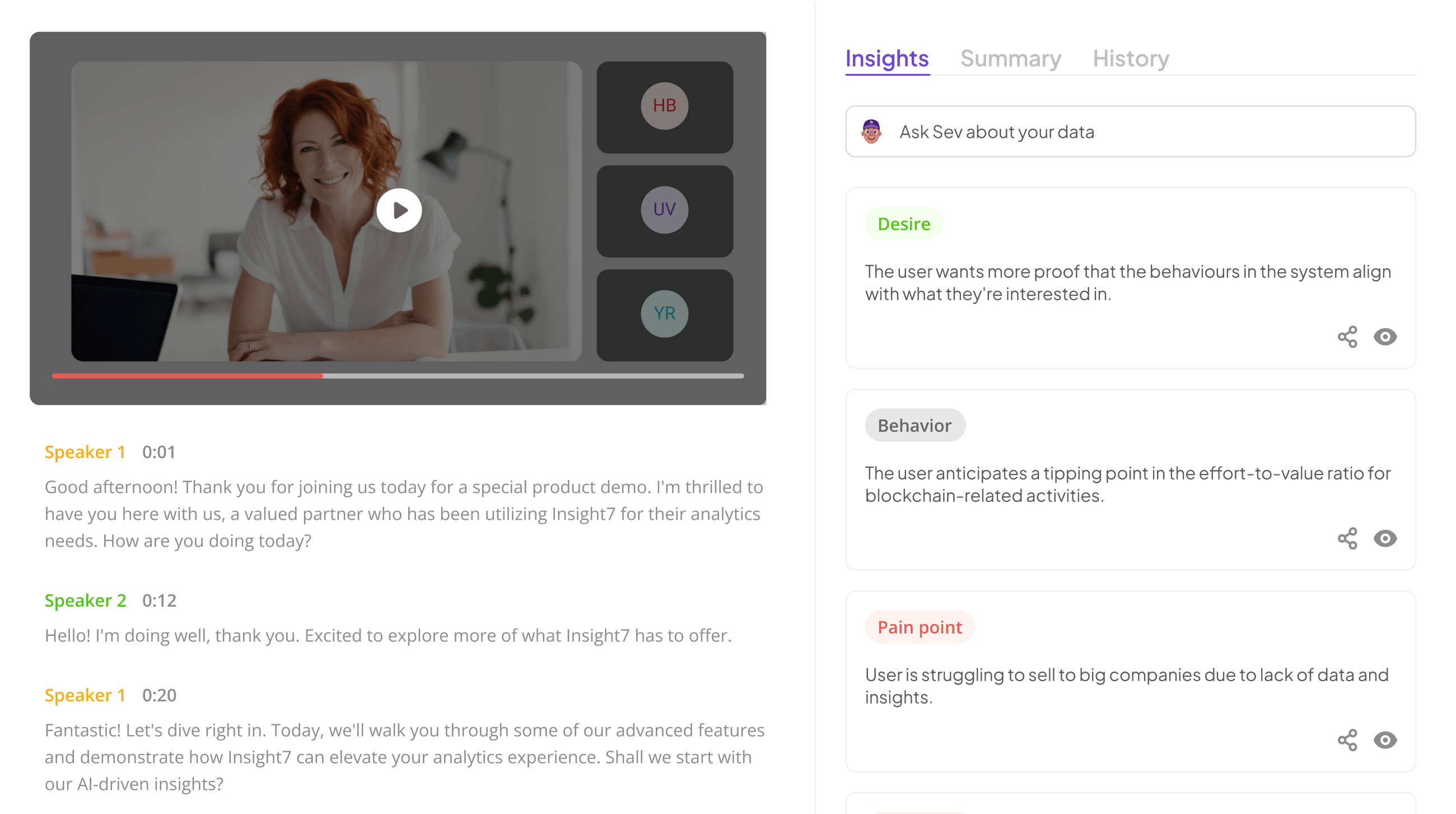
Recognizing the Calibration Mistakes Analysis in QA Sessions
Recognizing the Calibration Mistakes Analysis in QA Sessions is vital for refining quality assurance processes. Common errors often arise from misunderstandings or misalignments regarding quality standards. Variations in team members' interpretations of these standards can lead to inconsistent evaluations. To counter this issue, regular team discussions are essential for establishing a cohesive understanding of what constitutes quality. These conversations help bridge gaps in understanding and create a unified approach to QA assessments.
Additionally, inadequate training and a lack of appropriate tools hinder effective calibration. When team members do not receive proper training, they may struggle to apply quality standards effectively. It's crucial to equip teams with robust tools to facilitate accurate evaluations. Utilizing platforms like Insight7, Qualityze, and ZenQMS can enhance consistency in QA practices. Fostering a culture that emphasizes ongoing training paired with effective tools sets the stage for a successful Calibration Mistakes Analysis and ultimately leads to improved quality outcomes.
Calibrating QA sessions correctly requires precision and awareness. Here, we will explore the common errors that often slip through unnoticed.
Calibrating QA sessions correctly requires precision and awareness, as even the smallest oversight can lead to significant discrepancies in quality outcomes. Among the most common calibration mistakes are misalignments in quality standards. This gap can arise from team members having different interpretations of what quality entails. To avoid this, regular team meetings should be established to ensure everyone is on the same page regarding expectations.
Another frequent error stems from inadequate training and lack of necessary tools. Insufficient training can leave QA professionals ill-equipped to perform effectively, leading to calibration errors. Therefore, investing in comprehensive training programs is vital. Additionally, utilizing the right tools, such as Insight7, Qualityze, ZenQMS, MasterControl, and Qualio, helps in maintaining consistent QA standards. Thorough Calibration Mistakes Analysis focuses on these common oversights, paving the way for more effective QA calibration sessions and ultimately resulting in enhanced product quality.
Misalignment of Quality Standards
Misalignment of quality standards in QA calibration sessions often occurs when team members have differing perceptions of what constitutes quality. This discrepancy can lead to inconsistent evaluations and ultimately affect product outcomes. Regular team meetings can help ensure everyone is on the same page regarding quality expectations. By fostering open discussions, teams can clarify any misunderstandings and align their standards effectively.
Additionally, it’s essential to regularly revisit and document quality benchmarks to avoid the pitfalls of varying interpretations. Continuous dialogue helps maintain a uniform understanding of standards, reducing the likelihood of errors during the calibration process. Addressing this misalignment not only enhances the reliability of QA assessments but also reinforces the overall quality of the products being evaluated. Teams should prioritize establishing a clear and shared vision of quality standards as a vital component of their calibration mistakes analysis strategy.
- Discuss how differing understanding of quality standards can lead to inconsistencies.
Differing understandings of quality standards among team members can create significant inconsistencies during QA calibration sessions. When individuals interpret standards variably, the evaluation process suffers. This disagreement can lead to inaccurate assessments, ultimately affecting product quality. For instance, if one team member emphasizes customer satisfaction while another prioritizes compliance metrics, their evaluations will lack cohesion, undermining the calibration's effectiveness.
To mitigate these issues, fostering a common understanding of quality expectations is essential. One strategy is to hold regular team meetings focused on aligning criteria and discussing any ambiguities. Furthermore, documenting clear quality standards and evaluation criteria can serve as a guiding reference for all members. Ensuring everyone is on the same page is vital for achieving consistency in QA processes and avoiding calibration mistakes during analysis sessions.
- Suggest regular team meetings to align on quality expectations.
Regular team meetings are essential for aligning on quality expectations within QA calibration sessions. These meetings foster open communication and facilitate a shared understanding of quality standards among team members. As discrepancies often arise from differing interpretations of quality guidelines, consistent discussions help mitigate this issue.
To achieve effective alignment, consider scheduling these meetings weekly or bi-weekly. This frequency ensures that team members remain engaged and up-to-date with ongoing projects and perform Calibration Mistakes Analysis effectively. During these sessions, team members can discuss specific cases, evaluate past QA outcomes, and refine their approaches collectively. This collaborative atmosphere promotes a culture of accountability and commitment to quality, making it easier to track improvements over time. By continuously aligning quality expectations, teams can not only reduce calibration errors but also bolster product integrity and customer satisfaction.
Inadequate Training and Lack of Tools
Inadequate training and lack of tools are significant contributors to errors in QA calibration sessions. When team members are not properly trained, inconsistencies in understanding quality standards arise, leading to calibration mistakes. In these cases, agents may misinterpret performance metrics or fail to apply standards effectively during assessments. This not only hampers the quality of feedback provided to agents but can also undermine overall team confidence in the calibration process.
A crucial aspect of improving QA calibrations involves equipping teams with the right tools. Inconsistent or outdated tools can obstruct accurate evaluations. For example, utilizing platforms like Insight7 or Qualityze ensures standardized benchmarks throughout the calibration sessions. Additionally, ZenQMS, MasterControl, and Qualio offer comprehensive solutions that enrich the calibration process. Providing both adequate training and reliable tools fosters a supportive environment that minimizes calibration mistakes, promoting a culture of continuous improvement.
- Analyze how insufficient training can lead to calibration errors.
Insufficient training is a critical factor contributing to calibration errors in Quality Assurance (QA) sessions. When team members lack a comprehensive understanding of their roles and responsibilities, they may misinterpret quality standards or employ incorrect procedures. This misalignment can lead to inconsistent evaluations, impacting the overall effectiveness of the QA process. Moreover, without ongoing training, experienced team members may neglect to update their skills and knowledge, resulting in outdated practices being used.
To address this issue, it is essential to prioritize training programs that not only cover initial onboarding but also include regular updates to improve skillsets. Implementing a well-structured training curriculum ensures that all team members have the necessary knowledge to accurately assess and calibrate quality standards. Continuous education fosters a culture of professionalism and awareness, reducing the likelihood of calibration errors. Ultimately, investing in staff development is a proactive approach to improving QA calibration outcomes and maintaining product quality.
- Highlight the importance of using the right tools, including a list:
Using the right tools during QA calibration sessions is vital for reducing errors and maintaining quality standards. Proper tools enable teams to function effectively, ensuring consistent evaluation processes. The selection of suitable tools can significantly affect the outcome of Calibration Mistakes Analysis, helping identify discrepancies and streamline workflow.
Here are some essential tool recommendations that can enhance your QA calibration efforts:
- Insight7: This tool offers advanced analytics for ensuring consistent QA standards and supports data-driven decision-making.
- Qualityze: It helps in managing quality processes efficiently and ensures compliance with industry regulations.
- ZenQMS: This platform offers a seamless way to manage quality documents and workflows, improving overall efficiency.
- MasterControl: Recognized for robust quality management solutions, it focuses on streamlining documentation and compliance processes.
- Qualio: A modern tool that simplifies quality management tasks, enabling teams to ensure high standards effortlessly.
Choosing the appropriate tools will not only minimize errors but also foster a culture of continuous improvement within the QA process. Implementing these technologies facilitates better communication, training, and overall accountability, leading to enriched calibration sessions.
Tool Recommendations
In the context of effective QA calibration sessions, the right tools are essential to minimize common calibration mistakes. Utilizing specialized software can streamline the process and enhance accuracy. Some of the top recommendations are Insight7, Qualityze, ZenQMS, MasterControl, and Qualio. Each of these platforms brings unique features that facilitate consistent quality assurance practices.
Insight7 stands out as a leading choice for its user-friendly interface and robust analytics capabilities. Qualityze offers comprehensive solutions for document management, ensuring all team members are aligned. ZenQMS excels with its flexibility, making it suitable for a variety of industries. MasterControl provides extensive regulatory compliance support, while Qualio focuses on ease of use, simplifying the calibration process. By implementing these tailored tools, organizations can significantly reduce the risk of calibration errors, ensuring their QA sessions yield accurate and reliable results.
- Insight7: A leading tool for ensuring consistent QA standards.
To maintain consistent QA standards, Insight7 serves as a leading tool for Quality Assurance teams. The platform enhances Calibration Mistakes Analysis by enabling teams to analyze customer interactions effectively. By converting raw conversation data into actionable insights, Insight7 ensures that QA evaluators can consistently adhere to set quality benchmarks. This streamlined process helps organizations avoid common calibration errors that stem from miscommunication or inconsistent evaluations.
Moreover, Insight7 allows for data-driven decision-making. With its intuitive features, teams can identify trends in their quality assessments, fostering a more collaborative approach towards maintaining standards. The platform's capability to centralize QA data minimizes scattering, which often leads to inefficient collaboration among team members. By using Insight7, organizations can mitigate the risks associated with inadequate training and misalignment of quality expectations, ultimately achieving superior quality assurance outcomes.
💬 Questions about 5 Common Errors in QA Calibration Sessions?
Our team typically responds within minutes
- Qualityze
Qualityze is a crucial component in the realm of Quality Assurance (QA), particularly during calibration sessions. Effective calibration is essential for maintaining consistent quality across products and services. When organizations overlook the implications of calibration mistakes, they risk the integrity and reputation of their offerings. Understanding the importance of Qualityze allows teams to address errors proactively and align more closely with predefined standards.
In this context, the Calibration Mistakes Analysis highlights several potential pitfalls. One key mistake is the misalignment of quality standards, where team members have differing interpretations of what quality encompasses. Hosting regular meetings can help address this issue. Another critical error arises from inadequate training and lack of appropriate tools, making it essential for organizations to invest in effective QA solutions like Qualityze. Ultimately, recognizing these common errors and implementing tailored solutions can significantly enhance the accuracy and effectiveness of QA calibration sessions.
- ZenQMS
ZenQMS
ZenQMS plays a crucial role in enhancing the Quality Assurance (QA) calibration sessions. As organizations strive for excellence, understanding Calibration Mistakes Analysis becomes essential. ZenQMS is designed to streamline calibration processes, making it easier for teams to adhere to quality standards. This centralized platform allows for the efficient management of quality documentation and training materials, helping to eliminate common calibration errors.
One prevalent issue in QA is inadequate training, which can lead to misalignment in understanding quality expectations. ZenQMS offers robust training modules, ensuring every team member is equipped with the necessary knowledge. Furthermore, the tool provides analytics that highlight areas for improvement, allowing teams to track their calibration progress. By integrating ZenQMS into their QA environment, organizations can improve alignment on quality standards and ultimately enhance product outcomes. This proactive approach not only mitigates errors but also fosters a culture of continuous improvement, driving overall success in QA efforts.
- MasterControl
In the realm of Quality Assurance (QA), MasterControl serves as a vital tool for maintaining calibration standards. This platform offers integrated solutions that support the alignment of quality processes across teams. By utilizing MasterControl, organizations can expect reduced calibration mistakes and enhanced compliance with quality expectations.
One common error in QA sessions involves inconsistent understanding of quality standards, leading to varied evaluations among team members. MasterControl helps mitigate this issue by providing customized templates for evaluations, ensuring everyone adheres to the same criteria. Additionally, inadequate training often contributes to errors in QA calibration. MasterControl’s comprehensive training modules equip users with the necessary skills and knowledge, minimizing reliance on potentially flawed assumptions. Ultimately, leveraging MasterControl in your QA calibration sessions will foster a more uniform approach to quality assurance, leading to improved outcomes.
- Qualio
In the Calibration Mistakes Analysis, the role of tools is paramount for ensuring quality assurance alignment. One noteworthy solution stands out in providing an intuitive approach to calibration sessions. This platform facilitates the analysis of vast arrays of data and customer interactions in a manner that promotes accuracy and efficiency. It effectively addresses the challenges related to manual data handling, which can often result in errors or slowdowns.
Understanding how to optimize calibration sessions requires a systematic approach. First, it’s essential to identify the nuances in quality standards among team members. Different perceptions can lead to significant misalignments. Regular training sessions can bridge these gaps, while modern tools designed for QA calibration enhance the overall process. In summary, incorporating effective strategies coupled with the right technological support leads to a more robust calibration process, ultimately preventing common errors that compromise product quality.
Extract insights from interviews, calls, surveys and reviews for insights in minutes
Step-by-Step Calibration Mistakes Analysis: Addressing Top QA Errors
Effectively conducting a Calibration Mistakes Analysis involves a thorough investigation into the most common errors that can undermine quality assurance. First and foremost, it’s vital to recognize that misalignment in quality standards often leads to inconsistencies among team members. Implementing regular team meetings can help ensure everyone has a unified understanding of quality expectations and practices.
Another significant error arises from inadequate training and insufficient tools, which can compromise the calibration process. For effective calibration, providing comprehensive training ensures team members are well-equipped to evaluate performance accurately. Additionally, utilizing the right tools, such as Insight7, Qualityze, ZenQMS, MasterControl, and Qualio, enhances the calibration process. By systematically reviewing these errors and applying corrective measures, QA sessions can be optimized for better accuracy and higher standards in product quality.
Taking deliberate steps to improve QA calibration can drastically reduce errors. Below is a step-by-step guide to identifying and correcting common errors.
Taking deliberate steps to improve QA calibration can drastically reduce errors. A structured approach is crucial to ensure consistent quality in your QA sessions. Start by conducting comprehensive calibration reviews. This step involves regular assessments of QA processes, focusing on how well quality standards are implemented. Engaging your team frequently will help pinpoint misalignments and allow for prompt corrections.
Next, implement feedback loops for continuous improvement. Encouraging regular input from your QA teams helps identify areas needing attention. Encourage open communication about misunderstandings or obstacles faced during the calibration process. Addressing these issues collectively fosters a culture of accountability and progress. By focusing on Calibration Mistakes Analysis, your QA calibration sessions will become more effective, ultimately leading to improved product quality and higher customer satisfaction. These deliberate actions support sustainable quality assurance in any organizational setting.
Step 1: Conduct Comprehensive Calibration Reviews
Conducting comprehensive calibration reviews is essential for identifying and correcting calibration mistakes that often detract from the quality of QA sessions. This first step involves creating a structured approach where regular reviews are scheduled to ensure that quality standards are applied consistently. Begin by evaluating the criteria used during evaluations, checking if they align with the established quality benchmarks. Involving all team members in this process fosters a shared understanding of expectations, reducing the potential for errors caused by miscommunication.
Moreover, it is important to document findings from these reviews meticulously. By analyzing past calibration mistakes, teams can pinpoint recurring issues and develop targeted solutions. This Calibration Mistakes Analysis not only helps prevent future discrepancies but also provides valuable insights for enhancing training and ongoing support. Ultimately, comprehensive calibration reviews become the foundation for establishing a more effective and consistent QA process.
- Outline the process of regular reviews to ensure standards are accurately applied.
To ensure standards are accurately applied, it is vital to conduct regular calibration reviews in QA sessions. This process begins by establishing a clear schedule for when reviews will take place, typically on a monthly or quarterly basis. During these reviews, team members should analyze a selection of recorded calls or evaluations against predetermined quality criteria. This not only identifies calibration mistakes but also promotes a shared understanding of quality expectations among team members.
Next, it’s essential to gather feedback on these evaluations. Involving various team members helps reveal discrepancies in their assessments and allows for open discussion about improvements. This feedback loop should actively inform future training sessions and calibration standards. Consistent documentation of findings from each review aids in tracking progress and setting benchmarks for success. By embedding these practices, teams can significantly enhance their Calibration Mistakes Analysis, fostering a culture of quality and continuous improvement that leads to better product outcomes.
Step 2: Implement Feedback Loops for Continuous Improvement
Implementing feedback loops for continuous improvement is essential in refining the Calibration Mistakes Analysis process. By fostering a culture of open communication, teams can systematically identify pitfalls within QA calibration sessions. Feedback should be sought from various stakeholders, including QA analysts, supervisors, and team members. This collaborative approach encourages diverse perspectives, ultimately leading to more effective calibration practices.
Regular follow-up meetings after calibration sessions allow for real-time discussion of observed issues and suggestions for improvement. Documenting this feedback creates a historical reference for team members, highlighting which strategies proved successful and which did not. These documented insights can then inform training programs and operational adjustments. As a result, establishing robust feedback loops not only minimizes the likelihood of calibration mistakes but also contributes to a more agile and responsive QA environment, enhancing overall product quality.
- Detail the importance of receiving and integrating feedback from QA teams to improve calibration practices.
Receiving and integrating feedback from QA teams is essential for refining calibration practices. When QA professionals review calibration sessions critically, they bring attention to inconsistencies that might otherwise go unnoticed. Their insights illuminate common areas requiring improvement, thus enhancing the accuracy of evaluations. This feedback mechanism fosters a culture of continuous learning, where past mistakes inform future practices.
Moreover, regular integration of this feedback into calibration practices allows teams to adapt and evolve techniques based on real-world experiences. Frequent discussions on calibration trends and observations help align quality standards and clarify expectations. As adjustments are made, the QA team becomes more adept at identifying calibration mistakes, ultimately leading to a more precise calibration process. Emphasizing this collaborative approach not only strengthens the team's expertise but also enhances overall product quality.
Conclusion: Mastering Calibration Mistakes Analysis for Better QA
Improving Quality Assurance (QA) depends on acknowledging and addressing common calibration mistakes. Mastering Calibration Mistakes Analysis requires organizations to implement actionable strategies that enhance consistency and reliability. By identifying these errors, teams can focus on aligning quality standards and ensuring that every member is trained effectively.
To achieve better QA outcomes, continuous refinement and improvement are vital. Emphasizing regular feedback and calibration reviews allows teams to evolve their practices. Ultimately, mastering these techniques fosters greater accuracy, leading to enhanced product quality and overall customer satisfaction. Prioritizing Calibration Mistakes Analysis will significantly contribute to a successful QA process.
By focusing on a detailed Calibration Mistakes Analysis and taking actionable steps to rectify common errors, QA calibration sessions can achieve greater accuracy and consistency, leading to improved product quality and customer satisfaction.
To improve QA calibration sessions, focusing on a detailed Calibration Mistakes Analysis is paramount. Analyzing calibration mistakes allows teams to identify recurring issues that hinder the calibration process. These mistakes often stem from misunderstandings of quality standards among team members. By addressing these gaps, organizations can foster a greater sense of alignment, yielding more accurate outcomes.
Taking actionable steps is essential for rectifying these common errors. Regular team meetings can reinforce understanding and ensure everyone is on the same page regarding quality expectations. Additionally, implementing structured reviews can help pinpoint calibration inconsistencies before they escalate. By prioritizing these strategies, QA sessions become more effective, ultimately leading to improved product quality and increased customer satisfaction. The commitment to accuracy and consistency significantly impacts brand reputation and trust within the marketplace.
💬 Questions about 5 Common Errors in QA Calibration Sessions?
Our team typically responds within minutes